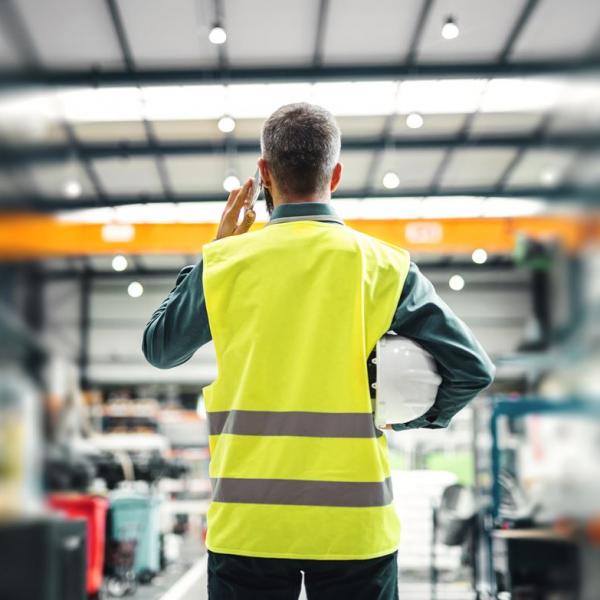
Operational Management
Motivated co-workers deliver the ordered high-quality products/services to our customers on time at expected or lower costs and they do so in a safe, eco-friendly, efficient, effective and structural way.
Operational management concerns the production of goods and services and ensures that the value adding activities within a company are run effectively and efficiently. It also means that the responsibility must be taken to consider and implement appropriate means. The right person with the right qualities needs to be at the right place. Operational management monitors stock levels, the supply of raw materials, logistical actions and the completion of the working load in due time. Here it is quite important to steer the company and to take proactive action e.g. by being on the shop floor every day in order to know what is happening on the work floor, rather than steering a department from an office. Also important is keeping discipline and making sure that a great atmosphere is being created. Co-workers need to be given sufficient responsibility to tackle any problems and to contribute significantly to improvement. A good communication between sales and operations leads to a better understanding and a correct way of anticipating. Operational management also deals with unexpected matters which require immediate action in order to learn lessons for the future. In this way, operational management is increasingly improving. Quality, safety, order and tidiness form the basis and should be kept in mind despite the sometimes high level of pressure.
What do I do on the customer side:
As an operational manager you will find me on the shop floor every day, because I want to know and feel what is happening on the work floor. By means of the KPIs I manage to make improvements clearly visible. And on the basis of monthly reports I also succeed in informing the top of the organisation about improvement areas. Good and adequate communication with all people involved is crucial and requires time.
Achievements:
- Product developer and work planner: imposing a realistic and attainable output for the production staff
- Safety advisor: integrating safety and well-being at work within the aspects of business operations
- Production manager: capacity control through adequate consultation with sales
- Plant manager: establishing KPI and drawing up a monthly operations report based on the daily output figures of OEE
- Operations manager: helicopter view on all facilities and exchange of capacity between the sites wherever necessary
Veelgebruikt model bij Operationeel Management: The House of Gemba
Gemba is een Japanse term en betekent oorspronkelijk “the real place”. Dit verwijst naar de plaats waar de waarde of oplossing voor een besluitvorming of verbetering wordt gevonden. The house of Gemba wordt vaak gebruikt in het bedrijfsleven wanneer bedrijven bijvoorbeeld knopen willen doorhakken, willen innoveren of veranderen.
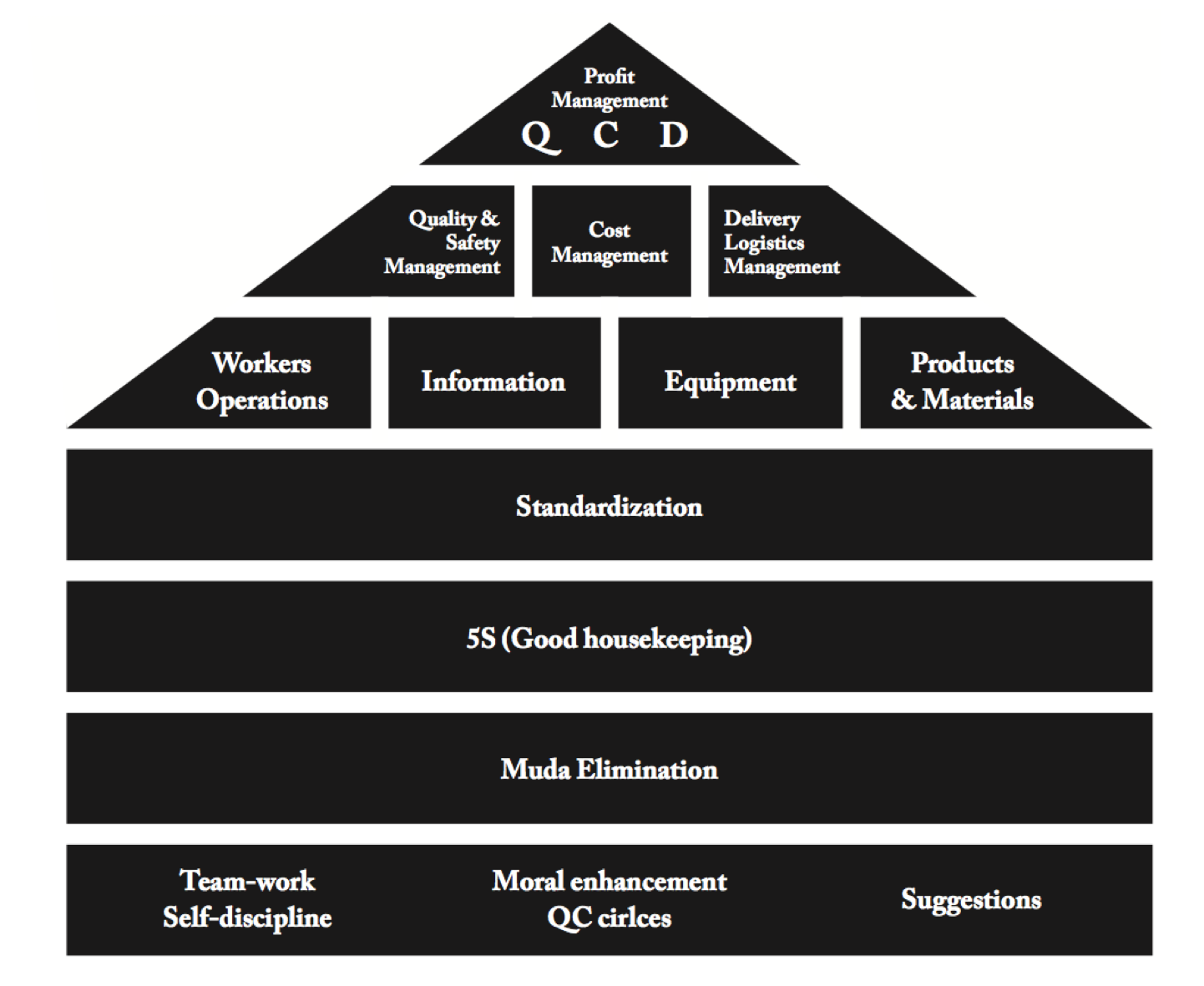